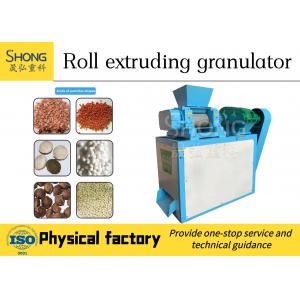
Add to Cart
The series of extrusion granulator drum type, its working principle is: motor driven belts, pulleys, through a reduction gear to a drive shaft, and synchronized by the open passive gear shaft, in one and the same working direction. Material was added from the hopper, by roll forming, release granulation; and crushing the ball transferred to the sieve chamber through a chain, the finished product (ball) was sieved and separated and then mixed back with the new material and re-granulated.
Technical Parameters
Model | DZJ-I 1.0 | DZJ-I 2.0 | DZJ-I3.0 | DZJ-I 4.0 | DZJ-II 1.0 | DZJ-II 2.0 |
Capacity | 1-1.5 | 1.5-2.5 | 2.5-3.5 | 3.5-4.5 | 1-2 | 1.5-2.5 |
Power | 15Kw | 18.5Kw | 30Kw | 45Kw | 15Kw | 18.5Kw |
Press Roller | Φ150×22O | Φ150×30O | Φ186×30O | Φ300×30O | Φ150×22O | Φ150×30O |
Feed Size | 0.5mm | 0.5mm | 0.5mm | 0.5mm | 0.5mm | 0.5mm |
Product Size | Φ2.5~Φ10 | Φ2.5~Φ10 | Φ2.5~Φ20 | Φ2.5~Φ20 | Φ2.5~Φ10 | Φ2.5~Φ10 |
Speed Reducer | ZQH350 | ZQH400 | ZQH400 | ZQH500 | ||
Material Mositure | 2%~5% | 2%~5% | 2%~5% | 2%~5% | 2%~5% | 2%~5% |
Granule Strength and Apperance Type:
Shape of finished products | oval, irregular, wheat shaped, etc., can also be customized according to customer requirements. |
Material moisture requirement | not more than 10% |
The rate of ball formation | 95% |
Output | 1-4t/h ( can combine multiple granulators work together to increase output, see below technical process chart). |
Granule size | 3-8mm (popular market granule diameter: 2.8-4mm) |
Product Introduction
Motor driven pulley, a belt through a reduction gear to a pair of two bodies with high pressure roller for relative sliding mode shell work.
DZJ-I extruder has two rollers, which interact split by the action of one pair of gears.
DZJ-II type two roll extruder directly driven by two dedicated output shaft gear, to achieve the purpose of the extrusion.
Production process, the raw material into the hopper, by a high pressure roller press molding body. After releasing the flow of crushed material a lower portion shaped rollers.
Break Dynamic formed by active pressing roller chain drive sprocket driven by one pair of crushing rollers relative movement.
After crushing and screening finished granules in the working chamber, through the screen to the discharge port outside the machine.